That’s an excellent project! Upcycling old jeans into a tote bag is a fantastic way to create a durable, stylish, and sustainable accessory. Jeans are perfect for this because their fabric is naturally sturdy, and you can incorporate existing features like pockets, seams, and even the waistband for a truly unique look.
This detailed guide will walk you through making a structured tote bag with a flat, boxed bottom and a full lining, utilizing the best parts of your old jeans.
How to Sew a Tote Bag from Upcycled Old Jeans
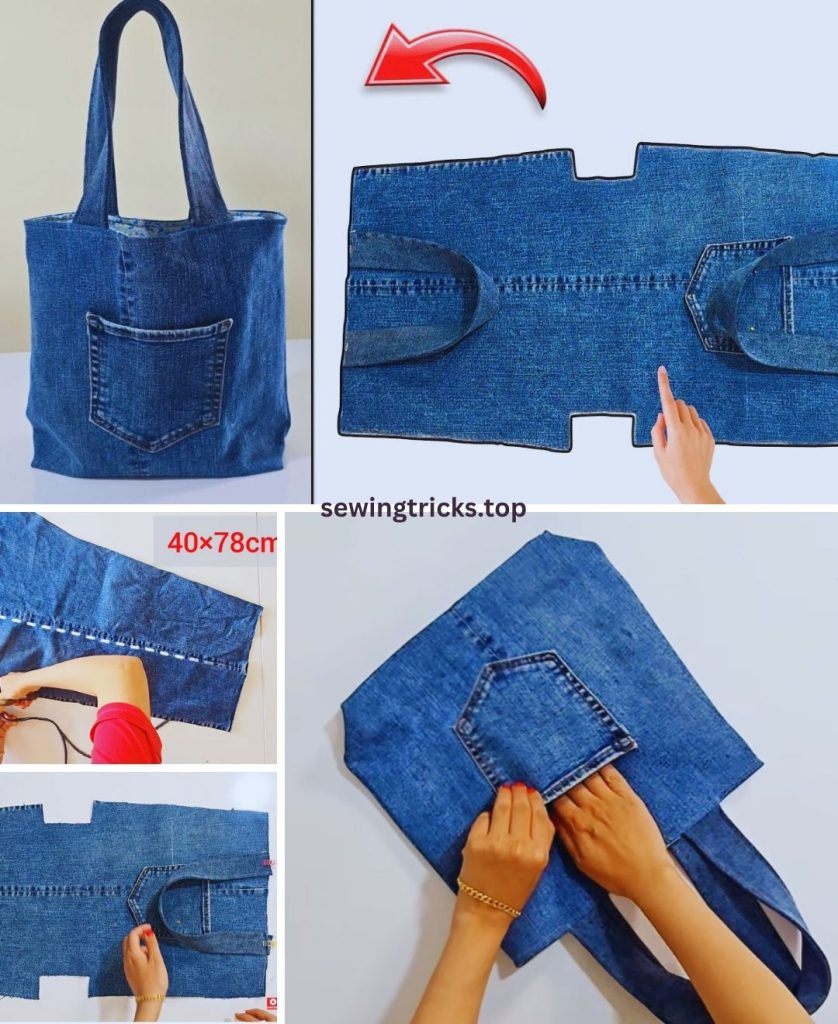
I. Planning Your Upcycled Denim Tote
Careful planning is crucial when working with repurposed materials, as it helps you maximize the usable fabric and anticipate any challenges.
- Choose Your Jeans Wisely:
- Size Matters: The larger the jeans (men’s large/XL, or women’s larger sizes), the more fabric you’ll have to work with, making it easier to cut larger panels without piecing.
- Fabric Type: Non-stretch or low-stretch denim is ideal. High-stretch denim can be tricky to sew and might result in a less structured bag.
- Condition: Ensure the jeans are clean, free of major stains (unless you want that worn-in look!), and ironed. Fading, rips, or patches can add character.
- Desired Tote Size: How big do you want your finished tote to be?
- Small (e.g., 10″ W x 12″ H): Great for a lunch bag or small project.
- Medium (e.g., 14″ W x 15″ H): A versatile size for everyday use, groceries, or books. This is a good target for most adult jeans.
- Large (e.g., 16″ W x 18″ H): Roomy carry-all. Might require fabric from two pairs of jeans or very large jeans.
- Key Denim Features to Reuse:
- Back Pockets: Easily detachable and can be topstitched onto the exterior of your new tote for instant utility and style.
- Waistband: Can sometimes be integrated as the top edge or a design detail.
- Original Seams: The thick, often topstitched seams (like the outseam or inseam) can be incorporated into your bag’s design for a cool, authentic denim look.
- Lining: Highly recommended for a professional finish, to hide raw seams, and to provide extra durability. You’ll likely need to supply new fabric for this.
- Handles:
- Fabric Handles: Made from the jean legs themselves or a coordinating sturdy fabric.
- Webbing Handles: Cotton or polyester webbing (1-inch to 1.5-inch wide) offers excellent durability.
- Stabilizer (Optional but Recommended): If you want your tote to have a firm shape and stand on its own, a sturdy interfacing is key.
II. Gather Your Materials
Having all your supplies ready before you begin will make the sewing process much smoother.
- Old Jeans: 1 pair of clean, ironed, sturdy denim jeans.
- Lining Fabric: 1 to 1.5 yards (0.9 to 1.4 meters) of medium-weight quilting cotton, broadcloth, or poly-cotton. Choose a fabric that complements your denim.
- Heavy-Duty Fusible Interfacing (ESSENTIAL for Structure!): 1 to 1.5 yards (0.9 to 1.4 meters) of medium to heavyweight fusible interfacing (e.g., Pellon 809 Decor Bond, Pellon 71F Peltex II Ultra Firm). This is critical for giving your bag a professional, structured shape.
- Handle Material:
- For Fabric Handles: An additional 1/2 yard (0.45 meters) of sturdy fabric (can be from the jeans if you have enough, or new coordinating fabric).
- For Webbing Handles: 1.5 to 2 yards (1.4 to 1.8 meters) of 1-inch or 1.5-inch wide cotton or polyester webbing.
- Matching Thread: Strong, all-purpose polyester thread. For topstitching on denim, use a slightly thicker topstitching thread in a contrasting color (like gold, orange, or beige) for an authentic look.
- Basic Sewing Supplies:
- Sewing Machine: Must be able to handle thick layers. A walking foot is highly recommended as it helps feed thick fabric layers evenly.
- Heavy-Duty Needles: Denim needles (size 90/14 or 100/16) are essential for piercing thick denim. Have spares on hand, as they can break.
- Sharp Fabric Scissors or Rotary Cutter and Mat.
- Long Quilting Ruler or Measuring Tape.
- Fabric Chalk or Mark-B-Gone Pen.
- Plenty of Wonder Clips (these are superior to pins for holding thick denim layers securely).
- Iron and Ironing Board (crucial for pressing seams and fusing interfacing).
- Seam Ripper (your absolute best friend for taking apart jeans!).
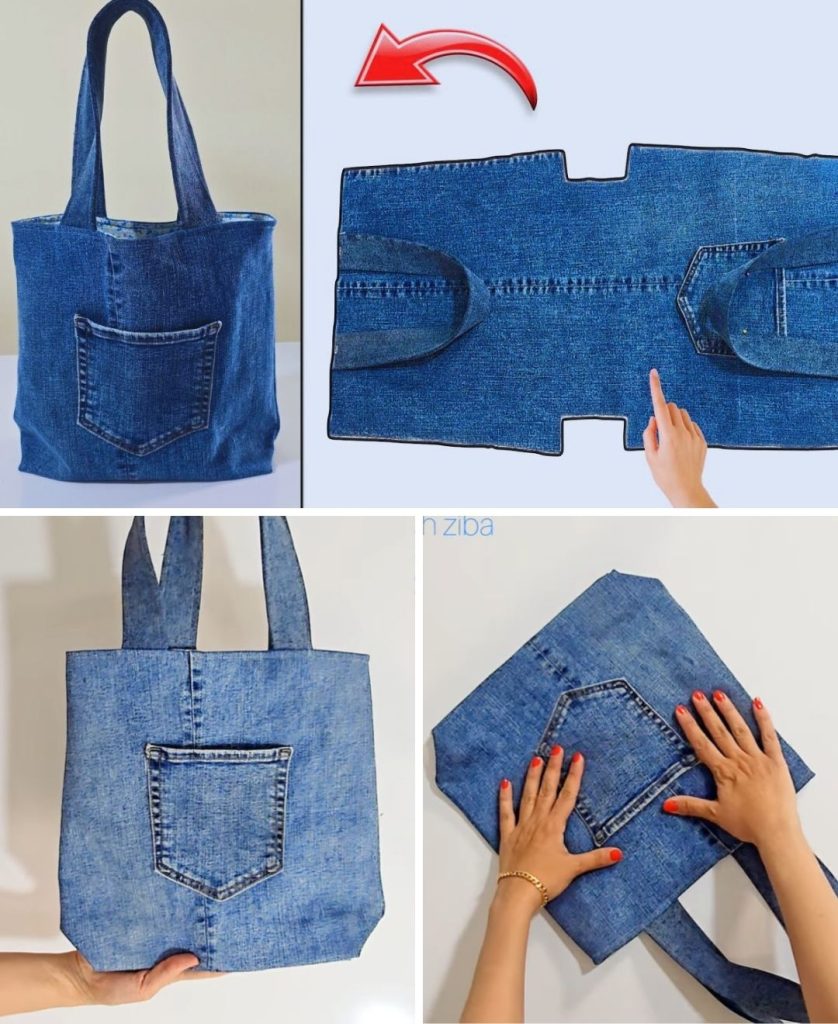
III. Prepare Your Jeans & Cut Fabric Pieces
This is the most time-consuming but crucial part of upcycling. Be patient and careful with your seam ripper!
A. Deconstruct Your Jeans:
- Cut Off Legs: Lay the jeans flat and smooth. Using your sharp fabric scissors, cut straight across both pant legs, just below the crotch seam.
- Open Leg Seams: Use your seam ripper to carefully open up both the inseam (inner leg seam) and the outseam (outer leg seam) of each cut-off leg. This will give you two large, flat panels of denim fabric. Iron these pieces flat to remove any creases.
- Harvest Back Pockets (Optional): If you plan to use the original back pockets on your tote, carefully seam rip them off the jeans. Try to keep them as intact as possible.
- Save Waistband (Optional): If you want to integrate the waistband into your bag’s design, carefully cut it off the jeans, keeping it intact.
B. Determine Your Bag Dimensions (Example: Medium Tote – 14″ W x 15″ H x 4″ D):
We’ll use a 1/2-inch (1.27 cm) seam allowance throughout the project.
- Main Body Panel Width: Finished Width + Finished Depth + (2 * Seam Allowance) = 14″ + 4″ + 1″ = 19 inches (48.3 cm)
- Main Body Panel Height: Finished Height + Finished Depth + (2 * Seam Allowance) = 15″ + 4″ + 1″ = 20 inches (50.8 cm)
C. Cut Your Fabric Pieces:
- Exterior Bag Pieces (from your jeans):
- Main Body: Cut 2 rectangles, each 19 inches wide x 20 inches high.
- Important Note on Piecing: It’s highly likely you’ll need to piece together sections of your opened-up jean legs to achieve these large panel dimensions.
- How to Piece Denim:
- Lay out your opened jean pieces. Strategically arrange them to get the most out of your fabric, considering the direction of any existing fades or unique denim characteristics.
- Place two denim pieces right sides together, aligning a long raw edge.
- Stitch them together using a 1/2-inch (1.27 cm) seam allowance.
- Press the seam open thoroughly to reduce bulk.
- Topstitch (Highly Recommended!): On the right side of the fabric, sew two parallel lines of stitching, one on each side of the seam line, about 1/8 inch (0.3 cm) away. Use your topstitching thread for this. This mimics authentic jean seams and adds immense strength and a professional finish.
- Continue piecing until you have two panels large enough for your final cuts.
- Main Body: Cut 2 rectangles, each 19 inches wide x 20 inches high.
- Lining Fabric Pieces:
- Main Body: Cut 2 rectangles, each 19 inches wide x 20 inches high.
- Interior Slip Pocket (Optional): Cut 1 rectangle, 10 inches wide x 12 inches high.
- Heavy-Duty Fusible Interfacing:
- Main Body: Cut 2 rectangles, each 18 inches wide x 19 inches high (1 inch smaller on all sides than your main denim panels to keep bulk out of the seam allowances).
- Handle Material (if using new fabric):
- Cut 2 rectangles, each 4 inches wide x 25 inches long. (You can try to use denim scraps if you have long, clean pieces, but new fabric might be easier).
- Webbing Handles: If using, cut 2 lengths, each 18-25 inches (46-63.5 cm) long (total 36-50 inches / 91.5-127 cm).
IV. Let’s Start Sewing Your Upcycled Denim Tote Bag!
General Sewing Tips for Denim:
- Always use a fresh, sharp denim needle. It makes a huge difference.
- Use your walking foot. It prevents stretching and ensures even feeding of thick layers.
- Go Slow! Stitch slowly, especially over existing jean seams or pieced areas. You might need to gently hand-crank your machine over particularly thick spots.
- Wonder Clips are better than pins for thick denim, as pins can distort the fabric or be hard to push through.
- Press, Press, Press. Pressing seams open after each step is vital for reducing bulk and getting crisp results. Use a good, hot iron.
- Topstitching: Use a slightly longer stitch length (3.0-3.5mm) for all topstitching to get that characteristic denim look.
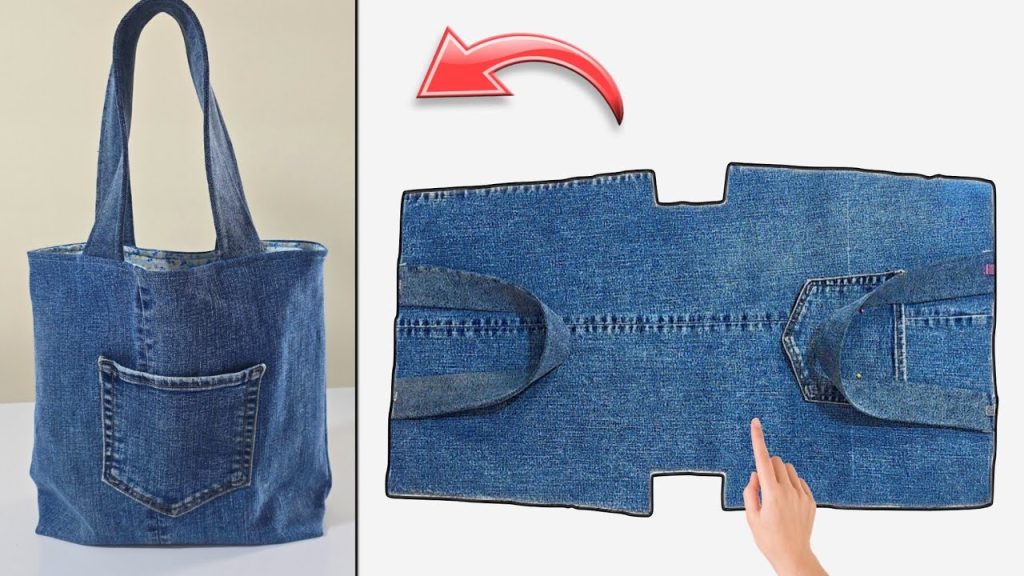
Step 1: Prepare Exterior Denim Panels (Fuse Interfacing & Add Optional Pockets)
- Fuse Interfacing: Take your two Exterior Denim Main Body Panels. Lay each one wrong side up on your ironing board. Center and fuse the corresponding Interfacing piece to each panel, following the manufacturer’s instructions. Press firmly and allow to cool completely. This is what will give your denim tote its excellent structure and body.
- Add Exterior Pockets (Optional): If you salvaged back pockets from your jeans, now is the time to attach them. Position a pocket onto one Exterior Denim Main Body Panel (this will be the front of your bag). Topstitch the pocket in place along its two sides and bottom edge. Stitch close to the folded edge (about 1/8 inch / 0.3 cm). Reinforce the top corners of the pocket with a small triangle stitch or a few back-and-forth stitches, as this is a high-stress area.
Step 2: Construct the Exterior Denim Bag Body
We’ll use a 1/2-inch (1.27 cm) seam allowance.
- Place the two Exterior Denim Main Body Panels right sides together, carefully aligning all raw edges.
- Clip securely along both side edges and the entire bottom edge. The top edge remains open.
- Stitch from one top corner down that side, pivot sharply at the bottom corner, stitch straight across the bottom, pivot again, and stitch up the other side to the top corner. Backstitch at the beginning and end of your seam for security.
- Press your seams open thoroughly to reduce bulk.
Step 3: Box the Corners of the Exterior Denim Bag
This step creates the flat, defined bottom of your tote bag.
- Lay the exterior bag body flat. The side and bottom seams should be pressed open.
- At one of the bottom corners, carefully bring the side seam and the bottom seam together, aligning them perfectly. This action will naturally form a triangular shape at the corner.
- Measure from the tip of this triangle inward along the seam line a distance equal to half of your desired bag depth (e.g., for a 4-inch deep bag, you’ll measure 2 inches / 5 cm).
- Draw a straight line perpendicular to the seam at this measured point. This is your new stitching line.
- Clip firmly along this drawn line.
- Stitch precisely along the drawn line, backstitching securely at both ends.
- Trim the excess fabric from the corner, leaving about a 1/2-inch (1.27 cm) seam allowance beyond your new stitching line.
- Repeat this exact process for the other bottom corner of your exterior bag body.
- Result: Your exterior denim bag now has a structured, flat bottom. Keep it wrong side out.
Step 4: Sew the Lining Bag Body (with Optional Pocket)
The lining is constructed almost identically to the main bag, with one crucial difference for turning the bag right side out later.
- Prepare Interior Slip Pocket (Optional):
- Take your 10″ x 12″ pocket piece. Fold it in half, right sides together, so it’s 10″ x 6″. Stitch around three sides (the two long sides and one short side), leaving a 3-4 inch (7.6-10.2 cm) opening on the remaining short side (this will be the bottom of the pocket). Trim corners.
- Turn the pocket right side out through the opening. Push out corners neatly and press flat. Stitch the opening closed by machine (very close to the edge) or by hand using an invisible ladder stitch for a seamless finish.
- Position and Attach Pocket: Take one of your Lining Fabric Main Body Panels. Position the pocket about 4-5 inches (10-12.7 cm) down from the top raw edge, and centered horizontally.
- Topstitch the pocket to the lining panel along its two sides and bottom edge. Stitch close to the edge. Reinforce the top corners of the pocket with a small triangle stitch or a few back-and-forth stitches.
- Sew Lining Body:
- Place the two Lining Fabric Main Body Panels right sides together, aligning all raw edges.
- Clip or pin along both side edges.
- CRUCIAL STEP: For the bottom seam, you must leave an opening! Stitch down one side seam. Then, for the bottom seam, stitch approximately 3 inches (7.6 cm) from one side, then leave a 4-6 inch (10-15 cm) unstitched gap in the middle of the bottom seam. This opening is absolutely essential for turning the entire bag right side out later. After the gap, stitch for another 3 inches (7.6 cm) to reach the other side seam. Backstitch well at the start and end of the stitched sections around your opening.
- Stitch up the second side seam.
- Press your seams open.
- Box the Corners of the Lining Bag: Box the corners of your lining bag using the exact same method you used for the exterior bag (refer back to Step 3).
- Result: Your lining bag is now fully constructed, with that important turning opening. Keep it wrong side out.
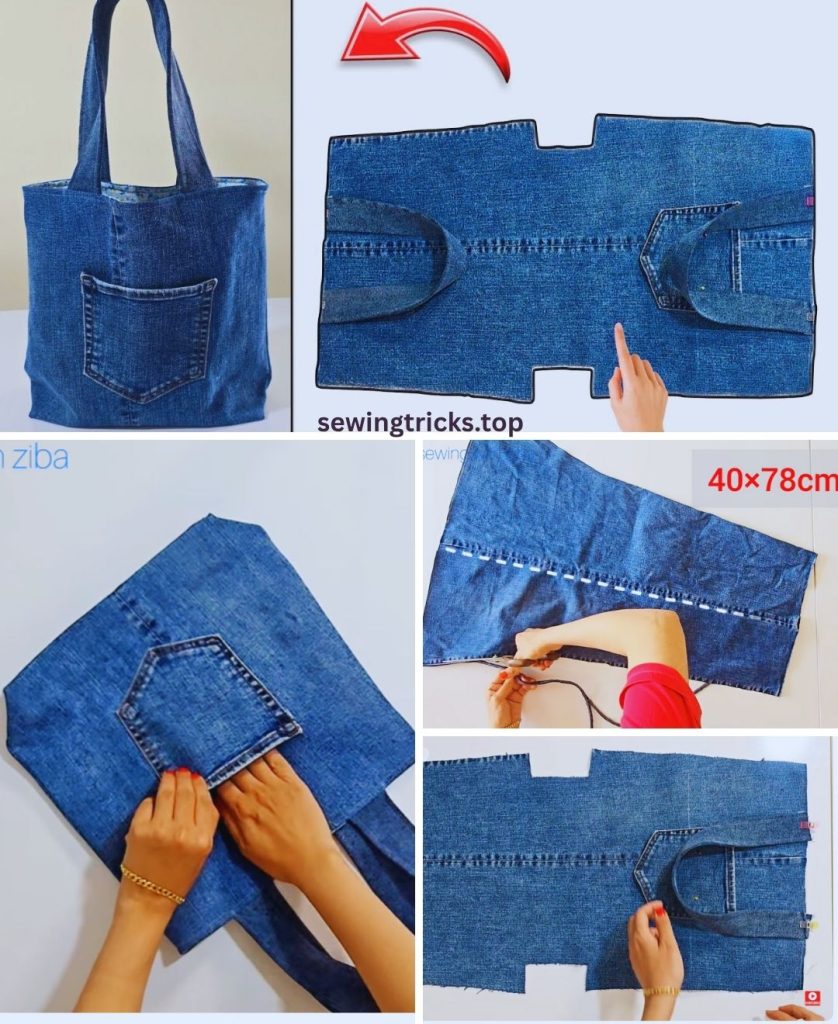
Step 5: Prepare and Attach Handles
A. If Using Fabric Handles (New Fabric or Denim Strips):
- Take one handle strip (4″ x 25″).
- Fold it in half lengthwise, wrong sides together, and press firmly. Open it up.
- Fold each long raw edge in towards the center crease you just made, and press again.
- Fold the entire strip in half again along the original center crease. You should now have a long, flat handle that is about 1 inch (2.5 cm) wide with no raw edges visible. Press firmly along the entire length.
- Topstitch down both long sides of the prepared handle, about 1/8 inch (0.3 cm) from the edge. Use your topstitching thread for this. This secures all the folds and makes a neat, strong handle.
- Repeat this process for the second handle strip.
- Attach to Exterior Bag: Turn your exterior denim bag right side out. Lay it flat, smoothing it out.
- Measure in from each side seam along the top raw edge by about 4-5 inches (10-12.7 cm). Mark these points with chalk.
- Position the raw ends of one prepared handle on the top raw edge of the bag at your marks. Make sure the handle itself is flat and not twisted. Clip securely.
- Stitch the handle ends in place. For a strong hold on denim, sew a small square (about 1×1 inch / 2.5×2.5 cm) with an “X” inside it (an X-box stitch) for maximum reinforcement. Stitch within the 1/2-inch (1.27 cm) seam allowance, close to the raw edge.
- Repeat for the other side of the bag with the second handle.
B. If Using Webbing Handles (New):
- Cut your webbing into two equal lengths (e.g., two 18-20 inch / 46-51 cm pieces).
- Attach to Exterior Bag: Turn your exterior denim bag right side out. Lay it flat.
- Measure in from each side seam along the top raw edge by about 4-5 inches (10-12.7 cm). Mark these points.
- Position one raw end of the webbing on the top raw edge of the bag at one mark, with the webbing loop pointing down into the bag. Clip securely.
- Stitch the webbing end in place using an X-box stitch for reinforcement. Stitch within the 1/2-inch (1.27 cm) seam allowance. Repeat for all four webbing ends (two ends per handle).
Step 6: Join the Exterior Bag and the Lining Bag (The “Bag-in-a-Bag” Method)
This clever technique encloses all raw edges at the top for a super clean and professional finish.
- Ensure your exterior denim bag is right side out, with handles attached and pointing down into the bag.
- Ensure your lining bag is wrong side out (and still has that turning opening at the bottom).
- Carefully insert the exterior denim baginto the lining bag.
- The right sides of both bags should now be facing each other.
- Align the side seams of the exterior bag with the side seams of the lining bag.
- Align the top raw edges of the exterior fabric and the lining fabric all around the entire opening of the bag. The handles should be sandwiched between the layers, pointing down.
- Clip very securely all the way around this top edge, matching up seams precisely.
- Using your 1/2-inch (1.27 cm) seam allowance, stitch all the way around the entire top opening of the bag. Go slowly and carefully, especially when you go over the handle attachment points (which will be very thick!). Backstitch at the beginning and end of your seam.
- Trim Bulk: Carefully trim the seam allowance at the top down to about 1/4 inch (0.6 cm) to reduce bulk inside the top edge.
Step 7: Turn Your Bag Right Side Out & Finish
This is the incredibly satisfying moment your upcycled denim tote bag takes its final, beautiful shape!
- Reach through the opening you left in the bottom seam of the lining.
- Slowly and carefully pull the entire bag (exterior, lining, handles – everything!) through this opening until it is completely right side out. Take your time, gently pushing out all the corners for a crisp, well-defined shape.
- Close the Lining Opening: Go to your ironing board. Press the raw edges of the opening in the bottom of the lining under by 1/2 inch (1.27 cm) so they meet neatly. Align these pressed edges and clip them together. Stitch this opening closed by machine (sewing very close to the folded edge for a neat finish) or by hand using an invisible ladder stitch for a truly seamless look.
- Now, push the lining down into the exterior denim bag.
- Final Press & Topstitch: Carefully press the entire top edge of the bag. Make sure the lining is fully tucked inside and isn’t peeking out over the top edge of the exterior fabric.
- For a super polished and durable finish, topstitch all around the entire top opening of the bag, about 1/8 inch (0.3 cm) from the edge. Use your topstitching thread for this. This final topstitching marries the lining to the exterior, helps the bag hold its shape, and creates a crisp, professional look. You can also sew a second row of topstitching about 1/2 inch (1.27 cm) from the top edge for added detail and stability.
Your unique, upcycled denim tote bag is now complete! You’ve transformed old jeans into a functional, durable, and stylish accessory that’s truly one-of-a-kind. Enjoy carrying your sustainable creation with pride!
What other upcycling or sewing projects are you thinking of trying?